The total manufacturing cost formula combines direct materials, direct labor, and manufacturing overheads to calculate production expenses. This guide will show you how to use it step-by-step for better financial insights.
Key Takeaways
- Total manufacturing costs encompass direct material costs, direct labor costs, and manufacturing overheads, crucial for effective financial management and decision-making.
- Understanding and accurately calculating total manufacturing costs allow businesses to identify inefficiencies, optimize production processes, and enhance profitability.
- Differentiating between direct and indirect manufacturing costs is vital for accurate financial reporting, helping companies manage their expenses and negotiate better supplier deals.
Table of Contents
- Understanding Total Manufacturing Costs
- The Total Manufacturing Cost Formula
- Practical Example of Total Manufacturing Cost Calculation
- Types of Manufacturing Costs
- Benefits of Calculating Total Manufacturing Costs
- Total Manufacturing Cost vs. COGM vs. COGS
- Streamlining Data Collection for Accurate Cost Calculations
- Summary
- Frequently Asked Questions
- Empower Your Manufacturing or Wholesale Business with OIS Solutions
Understanding Total Manufacturing Costs
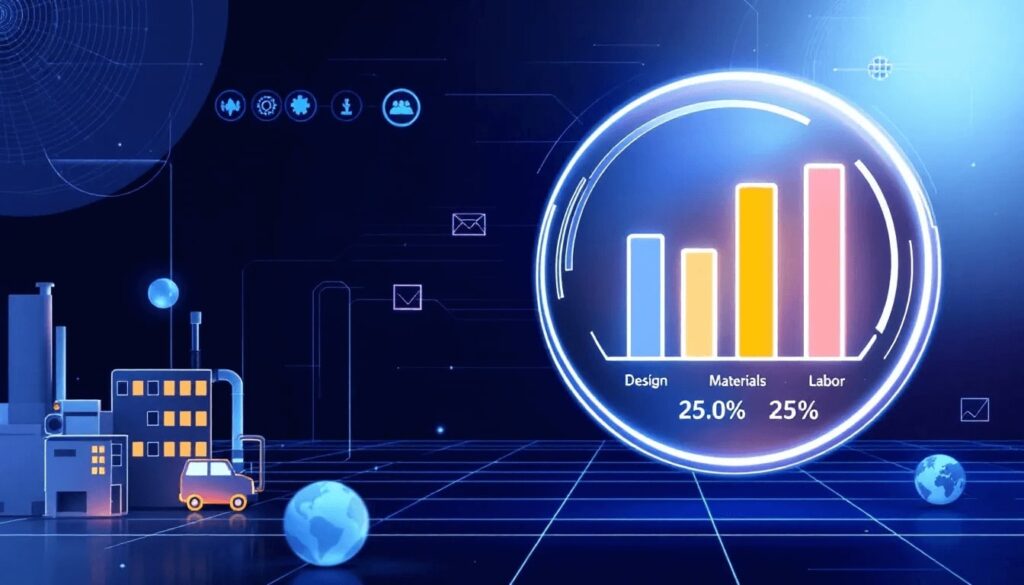
Total manufacturing costs represent the total amount spent on all production activities during a financial period. They encompass direct material costs, direct labor costs, and manufacturing overheads, providing a comprehensive assessment of resources committed to production. Understanding these costs is crucial for informed decision-making and better financial management. For instance, calculating total manufacturing costs helps businesses identify and rectify inefficiencies that may inflate production expenses.
Accurately determining manufacturing costs provides companies with clear financial statements, eliminating gaps in fund allocation. These insights facilitate better budgeting and financial planning, preventing underpricing and overpricing. By leveraging machine monitoring, manufacturers can gain real-time data on machine performance, helping refine cost estimations and reduce wastage. Moreover, understanding total manufacturing costs can uncover unnecessary expenses and highlight excessive costs, allowing businesses to negotiate better deals with suppliers.
A thorough grasp of all direct and indirect manufacturing expenses ensures accurate total manufacturing cost calculations. This understanding offers insights into production processes, aiding in improving efficiency, reducing waste, and increasing profitability. Low total manufacturing costs indicate efficient resource use, signaling a well-managed manufacturing operation.
The Total Manufacturing Cost Formula
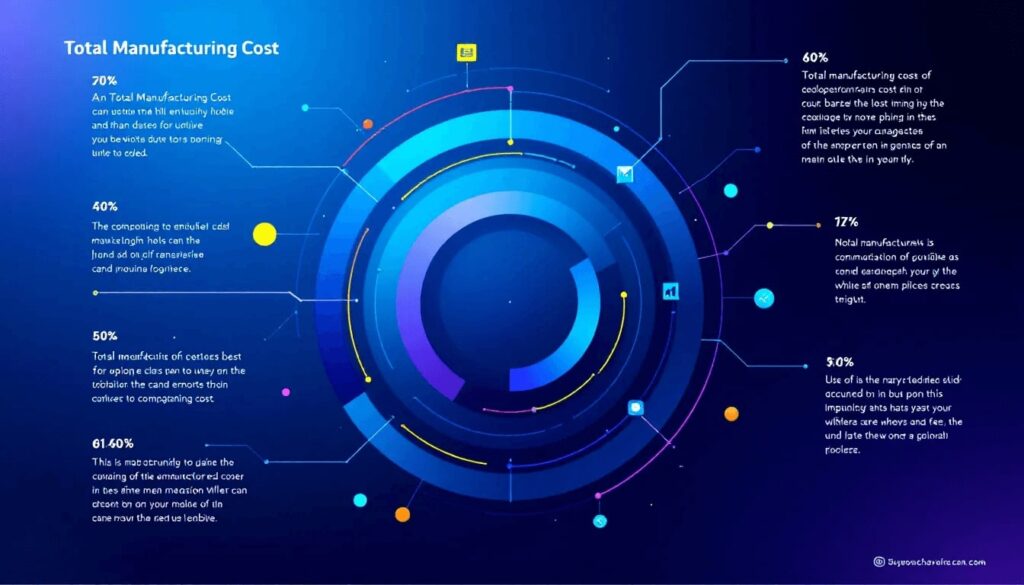
Calculating total manufacturing costs involves summing the direct material costs, direct labor costs, and manufacturing overheads. This formula provides a straightforward way to understand the total expense related to the production process. Total manufacturing cost consists of three primary components. These are direct materials, direct labor, and manufacturing overheads, and each one is critical for the calculation.
The initial step in calculating total manufacturing costs involves gathering accurate cost data, which is crucial for correct calculations. This process aids in evaluating profitability by comparing it with net revenue and provides insights into pricing strategies and cost control measures to calculate total manufacturing cost.
Applying the total manufacturing cost formula enables businesses to make informed decisions and optimize production processes.
Direct materials consist of raw materials and components. These can be directly traced to finished goods. The components of direct material costs include beginning inventory, purchased materials, and the value of materials that remain at the end of the period. To calculate direct material costs, use the formula: (Beginning direct materials + Purchased direct materials) – Ending direct materials.
For example, if you start with $2,500 of inventory and purchase $4,000 in materials but end with $2,000 in stock, the direct material cost is $4,500.
Strategies for reducing direct material costs include bulk purchasing and optimizing material usage. These strategies not only lower material costs but also contribute to overall cost efficiency in the production process.
Direct labor costs encompass wages and other expenses for personnel directly involved in manufacturing. To calculate these costs, multiply the hourly wage by the total hours worked on a project. This straightforward formula helps determine labor expenses and provides clarity on labor costs involved in production.
Additionally, direct labor costs can include benefits, holiday pay, payroll taxes, and training costs. To calculate direct labor costs per hour, use the formula: (Wages + Benefits + Additional labor expenses) / Total hours worked.
Accurate calculation of direct labor costs ensures that all expenses related to labor are accounted for, providing a clear picture of production costs.
Manufacturing overhead includes all indirect costs that cannot be directly attributed to the production of goods. These costs include rent, utilities, and maintenance needed for production. Examples of manufacturing overhead costs are factory utilities, rent, machine upkeep, and indirect materials.
Manufacturing overhead costs can be calculated by summing all indirect costs. These costs are then allocated to each product unit. Expenses such as energy bills, rent, machinery breakages, depreciation, repair and maintenance expenses, and production-related salaries are part of manufacturing overheads.
Allocating these costs accurately ensures precise financial reporting and effective cost control.
Practical Example of Total Manufacturing Cost Calculation
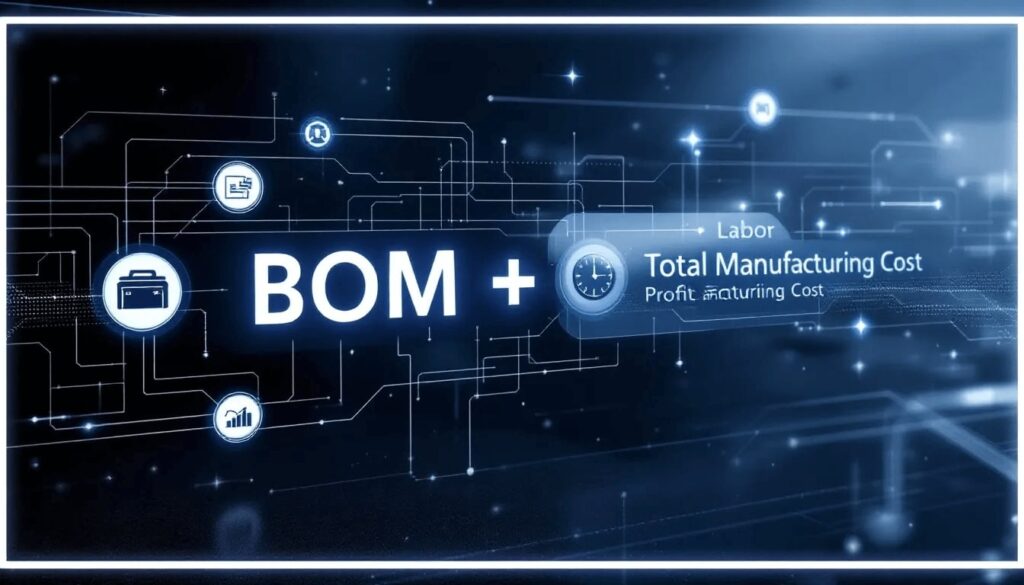
Let’s consider a practical example to illustrate the calculation of total manufacturing costs. Suppose we have the following hypothetical data: direct material costs of $5,000, direct labor costs of $4,000, and manufacturing overhead costs of $750. By adding these figures together, we get a total manufacturing cost of $9,750.
This example illustrates the simplicity and effectiveness of the total manufacturing cost formula. Accurate calculations provide businesses with insights into production expenses, aiding in informed decision-making to enhance profitability and efficiency.
Types of Manufacturing Costs
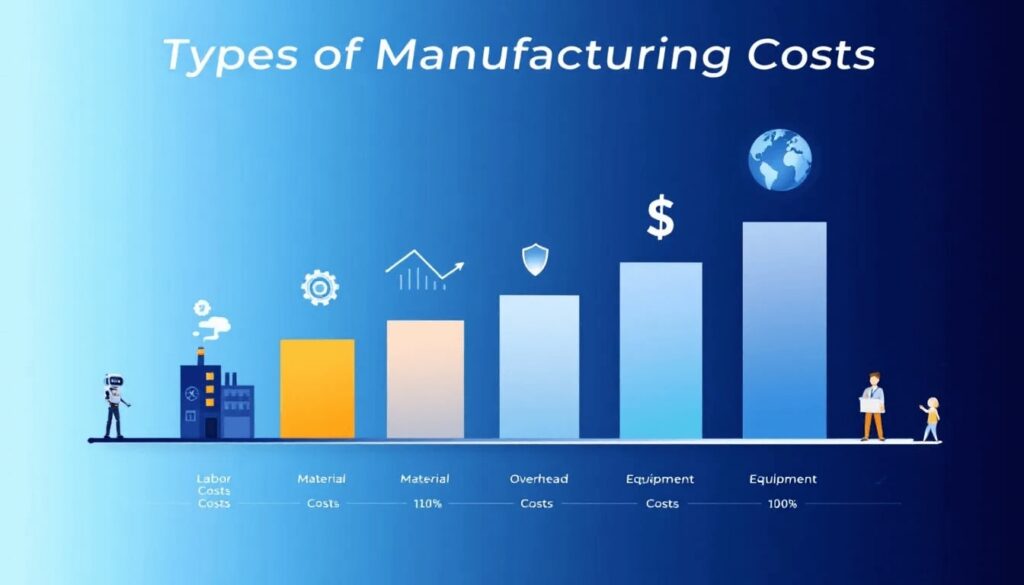
Manufacturing costs are categorized into direct and indirect costs, each playing a vital role in the overall cost structure. Direct costs are those that can be directly attributed to the production of goods, such as raw materials and production labor. Indirect manufacturing costs, on the other hand, support the overall operations necessary for production but cannot be traced directly to specific products.
Understanding the distinction between these two types of costs is crucial for accurate financial reporting and cost control. Direct costs tend to fluctuate with production volume, while indirect costs remain relatively stable, providing a comprehensive view of the expenses involved in manufacturing.
Direct costs are expenses that can be directly attributed to a specific product, such as production labor and raw materials. These costs are variable, meaning they increase or decrease based on the quantity of products manufactured. Direct manufacturing costs consist of direct labor and materials. Wages are also considered part of these costs.
Grasping direct costs is crucial for analyzing production expenses and making informed financial decisions.
Indirect costs in manufacturing are usually constant and fixed expenses like overheads. These costs, such as utilities and maintenance, support production but cannot be traced directly to specific units. Common indirect costs include administrative salaries and utilities, which benefit the operations as a whole.
Grasping indirect costs is vital for maintaining the overall financial health of the business.
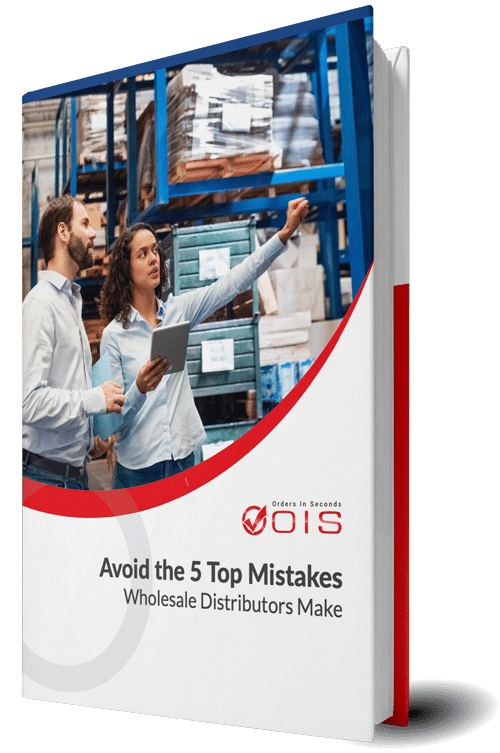
Avoid the Top 5 Mistakes Wholesale Distributors Make
Are you making one of the top 5 mistakes that plague wholesale distributors? Download our free eBook to find out. We’ve also included tips and guidance to help you save time and avoid costly mistakes.
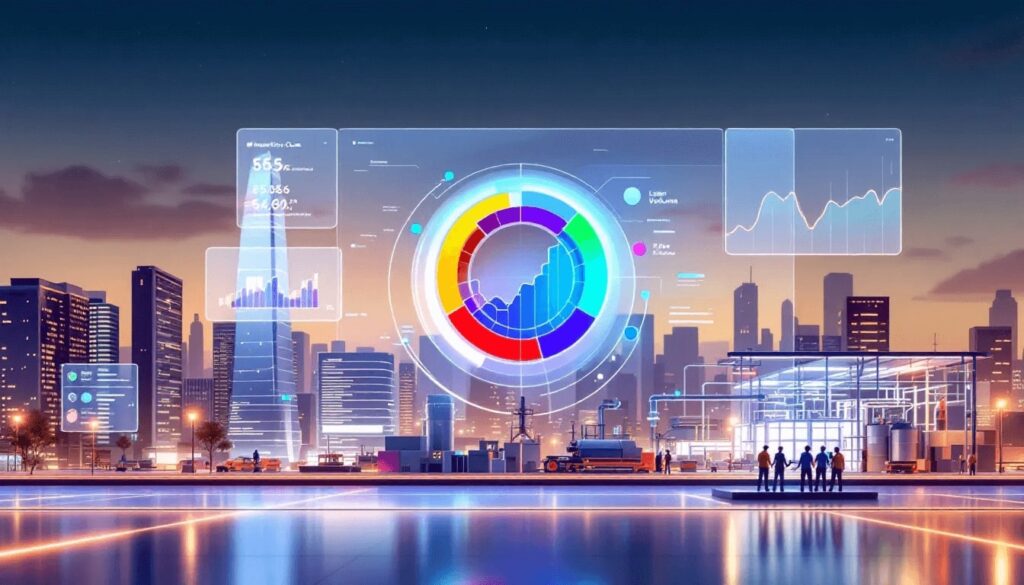
Knowing total manufacturing costs helps companies identify areas for improvement and efficiency. Analyzing these costs allows businesses to develop strategies for negotiating better deals with suppliers and setting competitive pricing strategies that reflect all production expenses.
Accurately calculating total manufacturing costs is essential for evaluating business profitability. It enables informed decision-making, optimization of production processes, and enhancement of financial health. These calculations offer benefits beyond cost control, impacting overall business success.
Total Manufacturing Cost vs. COGM vs. COGS
Total manufacturing cost encompasses all production-related expenses, critical for inventory valuation and other financial assessments. Cost of Goods Manufactured (COGM) indicates the total costs associated with completed goods ready for sale, derived from production expenses like direct labor and materials. Cost of Goods Sold (COGS) is calculated by adding COGM to the beginning finished goods inventory and subtracting the ending finished goods inventory.
While total manufacturing cost includes all expenses in production, COGM focuses on the costs of goods that are finished, and COGS pertains to the costs of those goods sold during a specific timeframe. Understanding the differences between these metrics is essential for accurate financial reporting and inventory management.
Streamlining Data Collection for Accurate Cost Calculations
Effective inventory management improves accuracy in manufacturing cost calculations. Implementing MRP systems aids in calculating direct material and labor costs by tracking purchases and summing reported work hours. These systems streamline data collection, ensuring all relevant costs are accurately recorded.
Accurate data collection methods are essential for calculating total manufacturing costs. Maintaining precise records of direct and indirect costs ensures financial statements reflect true production expenses, supporting better decision-making and financial planning
Summary
In summary, mastering the total manufacturing cost formula is essential for any manufacturing business. By understanding and accurately calculating direct material costs, direct labor costs, and manufacturing overheads, businesses can gain valuable insights into their production expenses. This knowledge supports better decision-making, cost control, and financial health.
Embrace the power of accurate cost calculations to optimize your production processes, reduce waste, and increase profitability. With the right tools and strategies, you can transform your manufacturing operations and achieve business success.
Frequently Asked Questions
Total manufacturing costs consist of direct material costs, direct labor costs, and manufacturing overheads. These components together represent the total expenses incurred in the production process.
To calculate direct material costs, use the formula: (Beginning direct materials + Purchased direct materials) – Ending direct materials. This ensures you accurately account for the materials consumed during a specific period.
Total manufacturing cost encompasses all production expenses incurred during the manufacturing process, whereas COGM specifically refers to the costs of goods that have been completed and are ready for sale. Therefore, COGM is a subset of total manufacturing cost.
Calculating total manufacturing costs enables businesses to identify inefficiencies and negotiate better deals with suppliers, ultimately leading to enhanced profitability. This practice also aids in setting competitive pricing strategies.
Empower Your Manufacturing or Wholesale Business with OIS Solutions
Accurate cost calculations are just the beginning. Orders in Seconds supports wholesale distributors and manufacturers with tools that simplify operations, enhance efficiency, and drive profitability. Whether it’s streamlining field sales with OIS Pro, managing order picking with OIS Inventory, or improving order delivery with OIS Delivery, we’ve got the solutions to help you succeed.
➡️ Explore OIS Solutions Today and see how we can transform your business.