Looking to improve your warehouse’s efficiency? Bin locations help by organizing inventory and saving time. This article explains how to optimize bin locations for a smoother operation.
Key Takeaways
- Effective bin location strategies enhance warehouse efficiency by minimizing search times, reducing errors, and improving inventory management.
- A systematic approach to bin labeling and organization, including unique identifiers and bulk bin creation, optimizes space and simplifies item retrieval.
- Incorporating technology for tracking and maintaining bin locations, along with regular audits and best practices, significantly increases operational accuracy and productivity.
Table of Contents
- Importance of Bin Locations in Warehouse Operations
- How to Create Effective Bin Locations
- Assigning Bin Locations
- Managing Bin Locations in Warehouse Transactions
- Managing Multiple Bin Locations
- Using Technology to Track Bin Locations
- Printing Labels for Bin Locations
- Setting Priorities for Bin Locations
- Optimizing Warehouse Space with Bin Locations
- Common Mistakes in Bin Location Management
- Best Practices for Bin Location Systems
- Summary
- Frequently Asked Questions
- Frequently Asked Questions
Importance of Bin Locations in Warehouse Operations
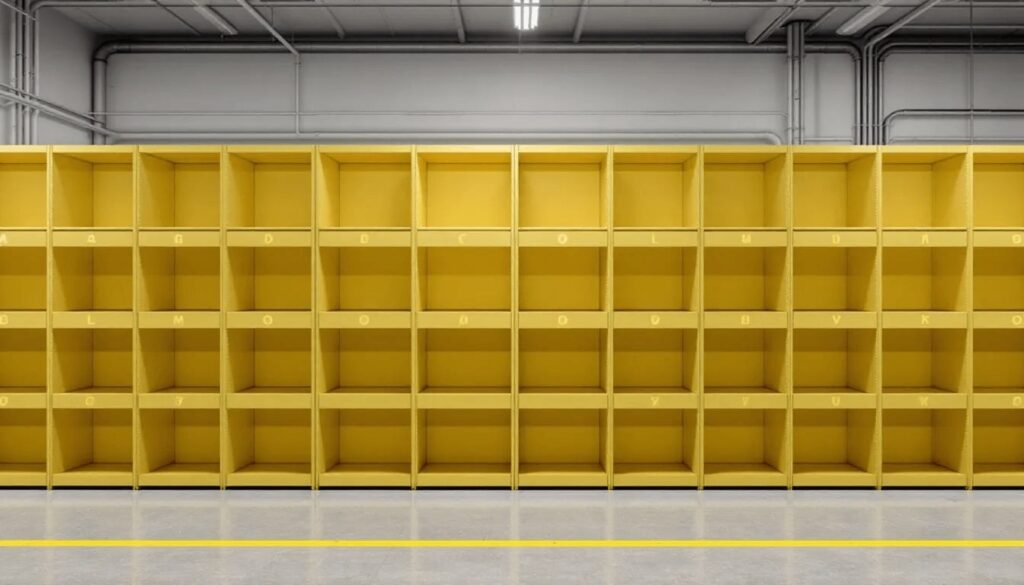
A warehouse bin storage system is the backbone of efficient operations in one warehouse, saving both time and money while significantly reducing errors. Providing specific locations for each item ensures accurate tracking and minimizes the chance of misplaced or lost inventory, maximizing storage space.
Dynamic slotting allows for the addition of new bins to optimize space and manage variable product turnover effectively.
Optimizing bin storage maximizes available space, reduces picker search time, and decreases mistakes. This efficiency improves accuracy and productivity, boosting profit margins. Proper bin labeling and tracking make order processing faster and more reliable, enhancing customer satisfaction and reducing storage costs.
Effective bin management prevents misplaced items and facilitates easy retrieval, streamlining the movement of goods. Organizing inventory with a unique bin location system allows staff to quickly find and correctly pick items, minimizing human error and enhancing operational efficiency.
How to Create Effective Bin Locations
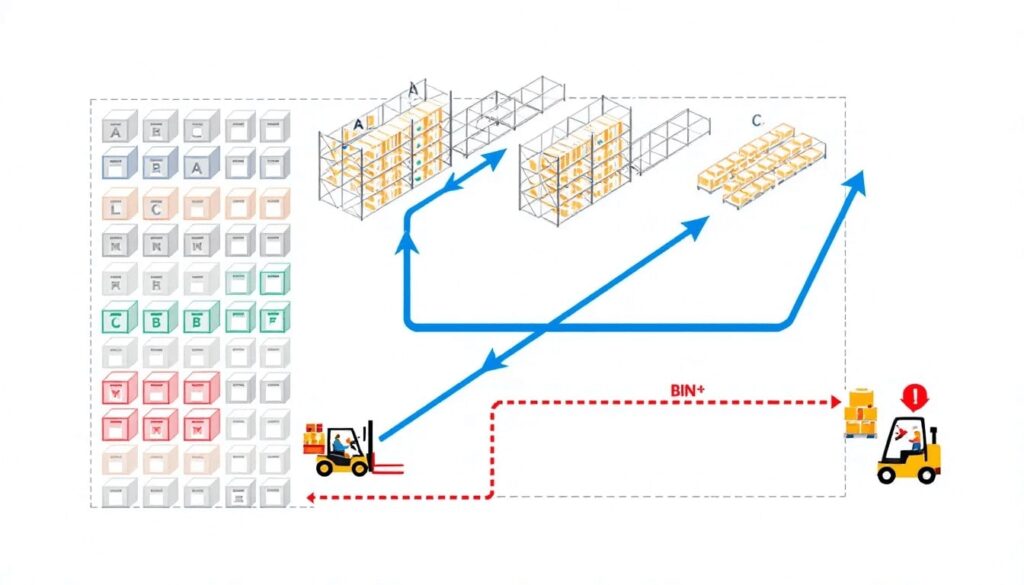
Creating an effective bin location system begins with a logical naming convention and considering the warehouse’s physical layout. Consistent naming simplifies item location and inventory management, while a well-planned layout ensures bins are easily identifiable and accessible. The flexibility to add new bins as required enhances the system’s effectiveness by optimizing space and managing variable product turnover efficiently.
This approach streamlines the retrieval process and significantly reduces order fulfillment time, ultimately leading to improved customer satisfaction.
Establishing short, clear naming conventions for individual bins ensures efficiency and quick identification. Each bin should have a unique alphanumeric identifier that avoids spaces, using dashes or underscores instead. This practice ensures every bin is easily distinguishable, aiding efficient tracking and retrieval, following a consistent naming convention.
Bins labeled as “A1-01-01” or “B2_03_02” are easy to read and locate. Unique identifiers prevent confusion and errors, allowing staff to manage inventory swiftly and accurately. This method lays the foundation for a more organized and productive warehouse.
Managing larger volumes of inventory efficiently requires bulk bin creation. Consistent naming conventions and alphanumeric codes make bulk bins easily identifiable and organized. Grouping similar items together optimizes space and improves retrieval times, allowing staff to locate and pick items quickly, even when managing multiple bins.
Regularly reviewing and adjusting bin locations based on inventory levels ensures continued efficiency. Consistent audits and staff training further enhance the effectiveness of bulk bin creation. This systematic approach reduces time spent on inventory organization and maximizes available space.
Assigning Bin Locations
Effectively assigning bin locations enhances inventory management. A structured bin location system allows for quick access and organized product storage, significantly reducing delays. Data analytics on inventory turnover can inform prioritization of high-demand products, ensuring they are easily accessible.
A first-in, first-out (FIFO) system helps manage product freshness and optimize inventory turnover. Color coding bins provides visual cues to quickly identify different product categories.
Dividing the warehouse into zones based on product characteristics, such as size and temperature needs, enhances operational efficiency by assigning specific storage bins to those regions.
Managing Bin Locations in Warehouse Transactions
Managing bin locations in warehouse transactions is crucial for efficient and accurate inventory management. Bin locations play a vital role in tracking and managing inventory, and their effective management can significantly impact warehouse operations. Here are some key considerations for managing bin locations in warehouse transactions:
Assigning Bin Locations: Assigning bin locations to specific items or product groups can help streamline warehouse operations. This can be done by creating a bin location system that is easy to understand and use. Clear and logical bin assignments ensure that items are stored in designated spots, reducing search times and improving overall efficiency.
Bin Location Codes: Using a consistent naming convention for bin location codes can help prevent errors and improve efficiency. Bin location codes should be unique and easy to read. For example, codes like “A1-01-01” or “B2_03_02” provide clear, unambiguous identifiers that facilitate quick and accurate item retrieval.
Enabled Bin Locations: Ensuring that bin locations are enabled for specific warehouses or storage areas can help automate inventory management processes. Enabled bin locations allow for seamless integration with warehouse management systems, enhancing operational efficiency and reducing manual errors.
Warehouse Locations: Defining warehouse locations and assigning bin locations to specific areas can help improve inventory tracking and management. By segmenting the warehouse into distinct zones, each with its own set of bin locations, you can optimize space utilization and streamline the movement of goods.
Storage Space: Optimizing storage space by using multiple bin locations can help reduce waste and improve operational efficiency. Multiple bins allow for better organization and categorization of inventory, ensuring that every inch of available space is utilized effectively.
Multiple Bins: Using multiple bins for different items or product groups can help prevent human error and improve inventory accuracy. This approach ensures that similar items are grouped together, making it easier for staff to locate and pick the correct products.
Available Space: Monitoring available space in bin locations can help prevent overstocking and improve inventory management. Regularly checking bin capacities ensures that there is always enough room for incoming stock, reducing the risk of overcrowding and misplaced items.
Print Labels: Printing labels for bin locations can help improve inventory tracking and management. Labels should include clear bin location codes and barcodes, making it easy for staff to identify and scan items during picking and restocking processes.
Specific Bins: Assigning specific bins to specific items or product groups can help improve inventory accuracy and reduce errors. This targeted approach ensures that each item has a designated spot, minimizing the chances of misplacement and enhancing retrieval efficiency.
Consistent Naming Convention: Using a consistent naming convention for bin locations can help improve inventory tracking and management. A standardized system simplifies the process of locating and managing inventory, reducing confusion and enhancing overall operational efficiency.
By implementing these strategies, warehouses can achieve significant improvements in inventory accuracy, operational efficiency, and overall productivity.
Managing multiple bin locations involves dividing the warehouse into zones based on attributes like package types, sales velocity, and activities. These zones can be designated for storage, packing, shipping, and receiving. Organizing the storage area into zones allows for logical grouping, making items easier to access and manage.
Placing fast-moving items closer to packing areas reduces picking times, improving overall efficiency. Assigning specific bins to distinct regions ensures systematic storage and quick retrieval, enhancing the effectiveness of the bin storage system.
Using Technology to Track Bin Locations
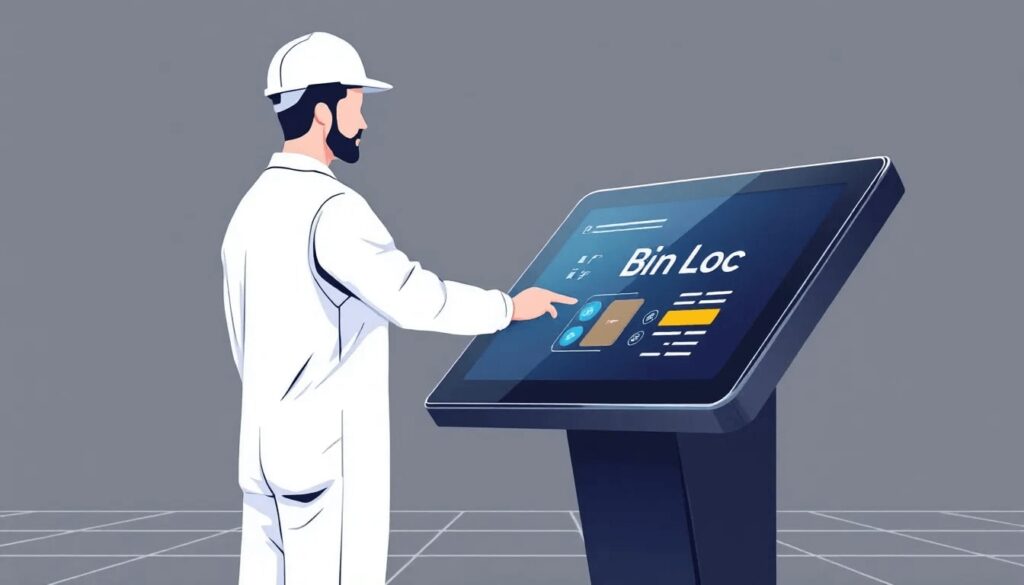
Incorporating technology into bin location tracking enhances warehouse efficiency. Manual inventory management often leads to inaccuracies, with as much as 35% of records affected by human error. Technologies like RFID and barcode scanners speed up data entry and reduce errors. A consistent coding format for bins, such as Zone-Aisle-Rack-Shelf-Bin, further streamlines inventory tracking.
Maintaining a comprehensive log of stored items aids in inventory tracking and minimizes errors. These technological solutions improve accuracy, save money and time, ultimately benefiting the business and its customers.
Efficiently tracking bin locations ensures accurate stock levels, crucial for timely order fulfillment and customer satisfaction.
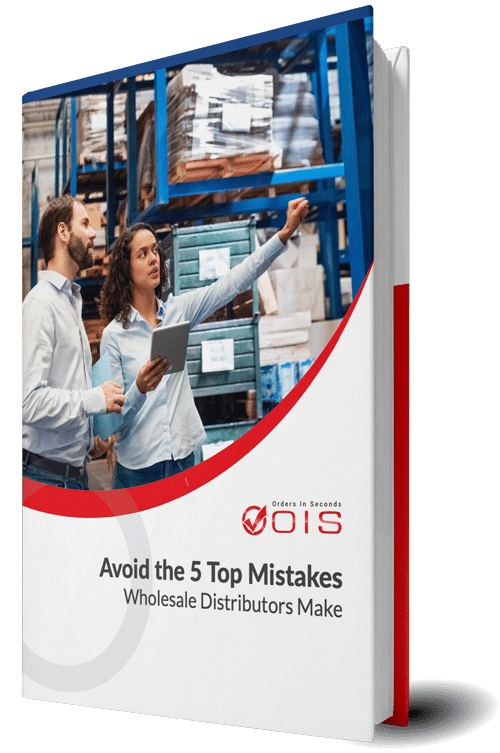
Avoid the Top 5 Mistakes Wholesale Distributors Make
Are you making one of the top 5 mistakes that plague wholesale distributors? Download our free eBook to find out. We’ve also included tips and guidance to help you save time and avoid costly mistakes.
Printing Labels for Bin Locations
Printing labels for bin locations is vital for maintaining an organized storage system. Standardized labels, including the Bin Name and a barcode, ensure clarity and consistency. Methods like using a Handheld Skustack device or Skustack Admin can print labels for location labels, with printer settings configured for proper output, including the bin location code.
Regular inspections and updates of bin labels maintain accuracy and prevent retrieval errors. Keeping labels legible and accurate is vital for operational efficiency. Rack labeling comes in two types: serpentine and standard, each catering to distinct organizational needs. Regular maintenance ensures they continue to support the bin location system effectively.
Setting Priorities for Bin Locations
Setting priorities for bin locations increases picking efficiency and reduces wait times. Creating a Restock List to replenish inventory from non-primary bins when primary bins lack sufficient stock ensures high-demand items are always available.
This prioritization maintains a smooth flow of operations and enhances overall productivity.
Optimizing Warehouse Space with Bin Locations
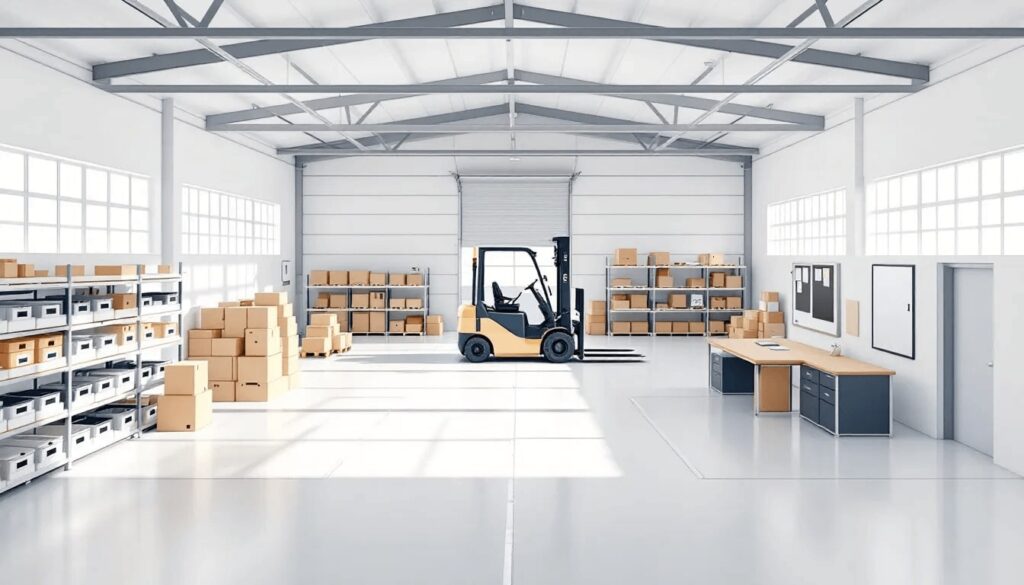
Optimizing warehouse space with bin locations in various warehouse locations reduces operational costs by minimizing the time spent finding and accessing products. Regularly reviewing bin utilization helps identify underperforming locations for restocking, enhancing efficiency. Implementing a bulk creation process for bins allows efficient setup across larger spaces, reducing time spent on inventory organization.
Adding new bins as required can help optimize warehouse space and manage variable product turnover effectively.
Designated areas for high-turnover items streamline picking processes and conserve space. Systematic organization maximizes available space and improves operational efficiency, ensuring smooth and effective warehouse operations, better inventory management, and cost savings.
Common Mistakes in Bin Location Management
Effective bin management is critical for maintaining accurate stock levels. Poor bin management can lead to stockouts and overstocking, negatively impacting operations. Removing bins no longer needed keeps the inventory system up-to-date. Enabled bin locations associated with transactions cannot be edited, disabled, or deleted, highlighting the importance of careful planning and management.
Grouping items by lot numbers enhances inventory control and improves traceability. This practice helps track product movement and ensures accurate stock levels. Avoiding these common mistakes leads to a more efficient and effective bin location management system.
Best Practices for Bin Location Systems
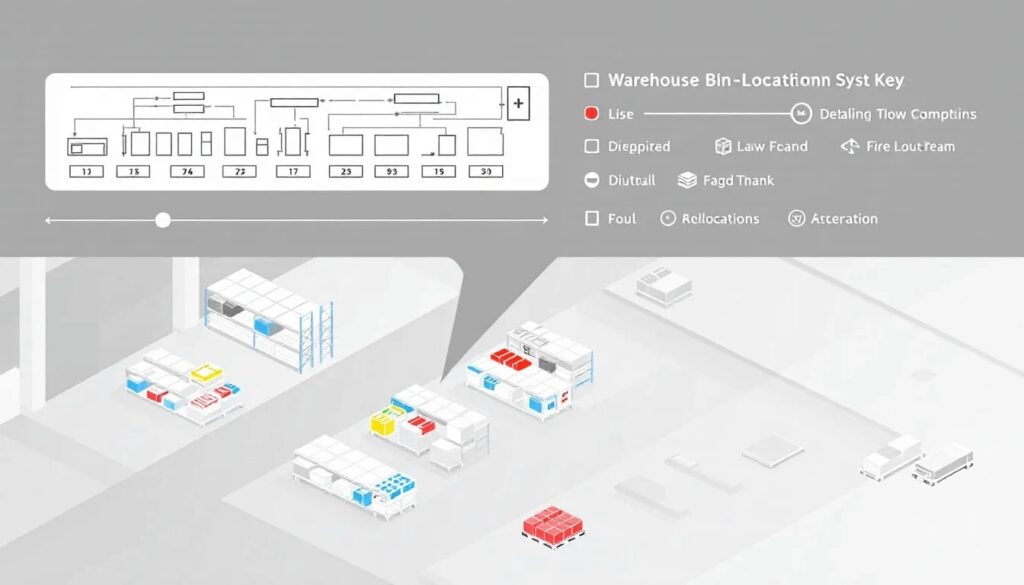
Adopting best practices for bin location systems enhances productivity and safety. Regular audits prevent overcrowding and ensure efficient use of space. Utilizing vertical space by stacking bins increases storage capacity, while a clear bin location strategy reduces accidents and enhances security.
A well-optimized bin location system enhances inventory accuracy and speeds up order fulfillment. Training staff on the labeling system ensures they understand how to read and interact with labels effectively. Labels should be durable enough to withstand the warehouse environment, including exposure to dust and varying temperatures.
Using a warehouse management system (WMS) improves organization by providing systematic logic for goods placement. A WMS allows quicker validation of inventory and improves stock level accuracy, enhancing operational transparency and efficiency.
Summary
In conclusion, an efficient bin location system is essential for optimizing warehouse space and enhancing overall productivity. By implementing best practices for creating, assigning, and managing bin locations, warehouses can achieve significant improvements in operational efficiency, inventory accuracy, and cost savings. Embrace these strategies to transform your warehouse into a well-organized, high-performing facility.
Frequently Asked Questions
A bin location system is essential for efficient warehouse management as it allocates specific storage locations for each item, facilitating improved tracking and retrieval of inventory. This system enhances operational efficiency and minimizes errors in stock handling.
Setting priorities for bin locations significantly enhances warehouse efficiency by ensuring that high-demand items are readily accessible, which minimizes picking time and reduces wait times. This strategic organization ultimately leads to a more streamlined operation.
Regular auditing of bin locations is essential to prevent overcrowding and ensure efficient space utilization, ultimately enhancing the overall efficiency of warehouse operations.
Technology plays a crucial role in tracking bin locations by utilizing RFID and barcode scanners, which enhance inventory accuracy, expedite data entry, and minimize human error, thereby optimizing warehouse operations.
Bulk bin creation significantly enhances warehouse management by improving inventory efficiency, reducing retrieval times, and optimizing space utilization through the grouping of similar items. This ultimately leads to a more organized and effective warehouse operation.
Pinpoint Every Product with Precision
Optimizing your warehouse begins with smarter bin location strategies. With the OIS Inventory App, your team can instantly locate products using precise bin location numbers—cutting down search time and boosting picking accuracy. Take control of your space and streamline operations. Schedule your demo today.