Looking for warehouse space for rent? Discover how to find and secure a warehouse that fits your business like a glove. Quick tips, direct insights, no detours. Unlock the right space, terms, and location for your logistics—your journey to an efficient warehouse starts here.
Key Takeaways
- Assessing warehouse space involves considering size, layout, and storage capabilities to ensure efficiency, with factors such as inventory size, workflow, and storage methods playing a crucial role.
- The location of a warehouse greatly impacts operational costs and customer satisfaction, with accessibility, transportation links, and proximity to customers and suppliers being key considerations.
- Understanding and negotiating the terms of warehouse lease agreements is essential, encompassing different lease types, associated costs, legal implications, and preparation for move-in.
Table of Contents
- Understanding Your Warehouse Needs
- Choosing the Ideal Location
- Exploring Different Types of Warehouses
- Navigating Lease Agreements
- Searching for Available Warehouse Spaces
- Evaluating Potential Warehouse Spaces
- Negotiating Lease Terms and Finalizing the Agreement
- Summary
- Frequently Asked Questions
- Optimize Your Wholesale Business Operations with Orders In Seconds
Understanding Your Warehouse Needs
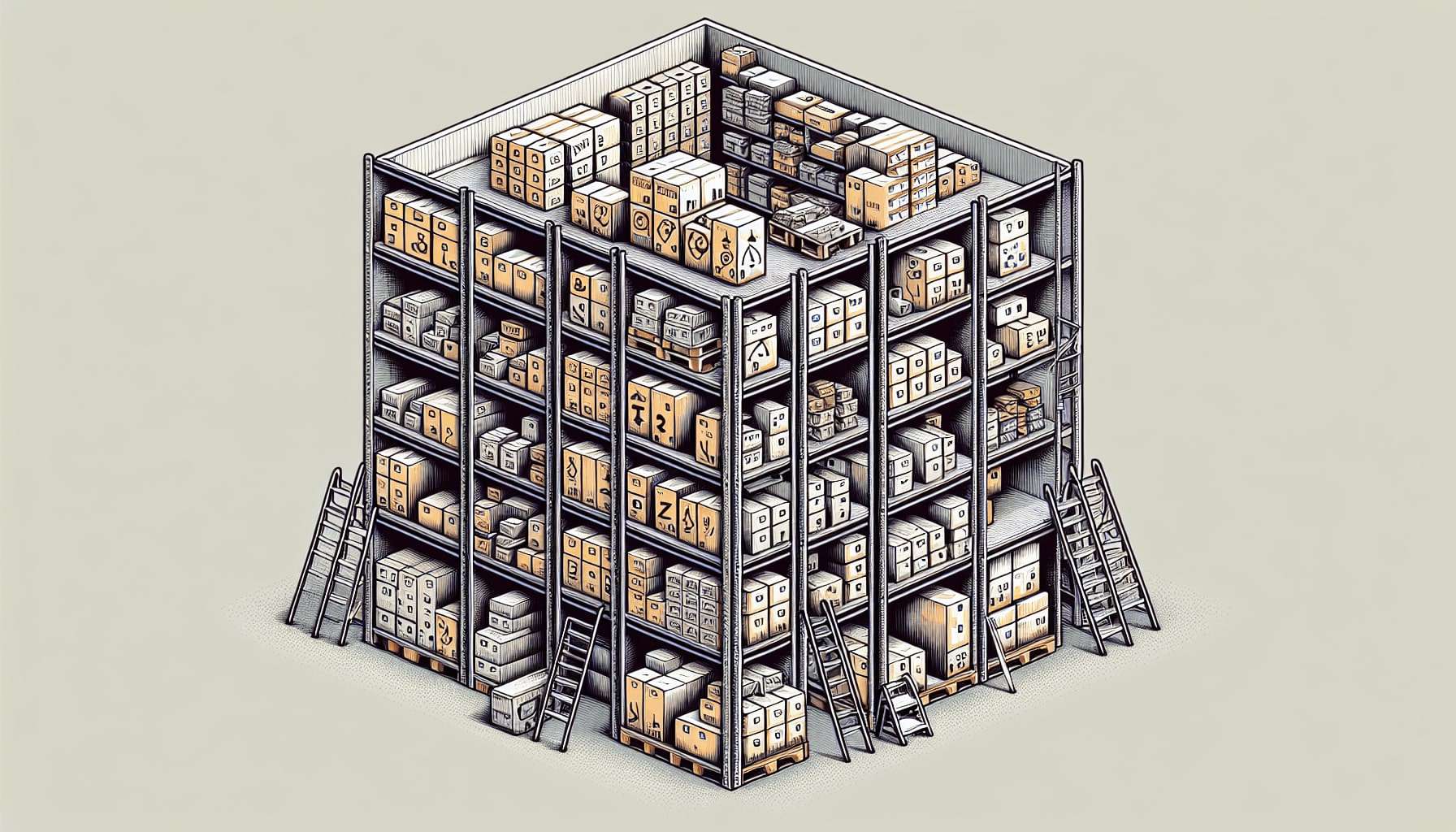
When it comes to warehouse leasing, one size does not fit all. Every business has unique needs that must be catered to. Small warehouse spaces might fit the bill for some, while others might need larger warehouses for lease.
But how do you determine what you need? The key is to consider the size, layout, and storage capabilities that align with your business operations. Adjusting your warehouse space to suit these needs guarantees functionality and efficiency.
Size and Space
Size matters when it comes to warehouses. The square footage needed for warehouse space should take into account areas for:
- Inventory storage
- Packing supplies
- Heavy equipment
- Staff workspace
- Loading areas
Creating a 2D visualization of the space and calculating the total storage area while adjusting for the utilization rate is a recommended strategy.
Consider the dimensions and stacking capacities of pallets and boxes, which affect the utilization rate of the warehouse. By accurately estimating space needs, you can avoid the common pitfall of renting a warehouse that’s too small or larger than necessary.
Layout and Design
Once you’ve determined the size of your warehouse, the next step is to consider the layout and design. An efficient layout optimizes the flow of goods from receiving to shipping, enhancing workflow and productivity. Key areas of warehouse layouts include:
- Receiving
- Storage
- Packing
- Shipping
- Office spaces
Each positioned to support an effective workflow, the performed triggered several actions, including an SQL command, to ensure efficiency.
Always communicate with your warehouse staff to identify potential hazards and gather insights to create a safer work environment, which contributes to overall efficiency.
Storage Capabilities
Last but not least, consider the storage capabilities of your warehouse. The space utilization rate helps evaluate the efficiency of the warehouse space needed based on how products are stored and their turnover rates. Utilization rates can be calculated with reference tables that consider product characteristics and storage efficiency, aiding in optimizing the space required.
Implementing effective storage solutions such as pallet racks and shelving units can facilitate easy access, efficient inventory management, and accurate order picking.
Choosing the Ideal Location
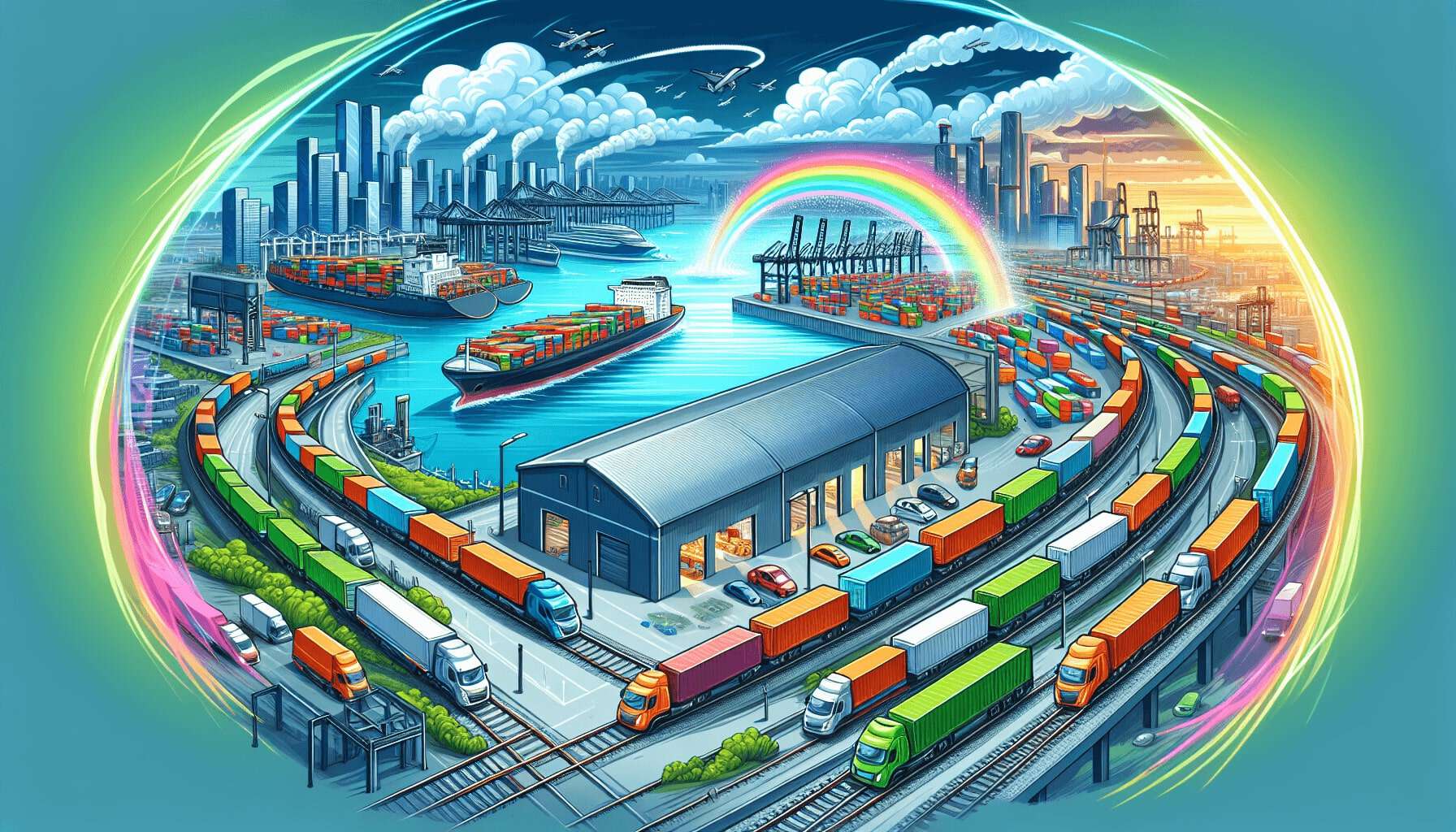
Once you’ve determined your warehouse needs, the next step is to choose the ideal location. The location of your warehouse can significantly impact your bottom line, affecting transportation costs, delivery times, and customer satisfaction.
An optimal warehouse location contributes to:
- Reduced shipping costs
- Improved efficiency
- Enhanced customer satisfaction
- Meeting customer expectations
Strategically selecting your warehouse location can lead to significant savings and improvements in overall business logistics.
Accessibility
Location isn’t just about being close to customers and suppliers; it’s also about accessibility. A strategic warehouse location requires good transport links for effective delivery operations and ease of access by clients, including connectivity to:
- major highways
- railways
- waterways
- air routes
Efficient movement of goods is facilitated by warehouses situated near robust transportation networks that encompass highways and railroads, ensuring swift and reliable transit. Local traffic patterns and road conditions should not be overlooked, they can significantly affect transit times and potentially increase transportation costs if not optimal.
It’s essential to pay attention to your approach to route management, as many overlook this factor, which can be a big mistake. Learn more in our free eBook “Avoid the 5 Mistakes Wholesale Distributors Make”.
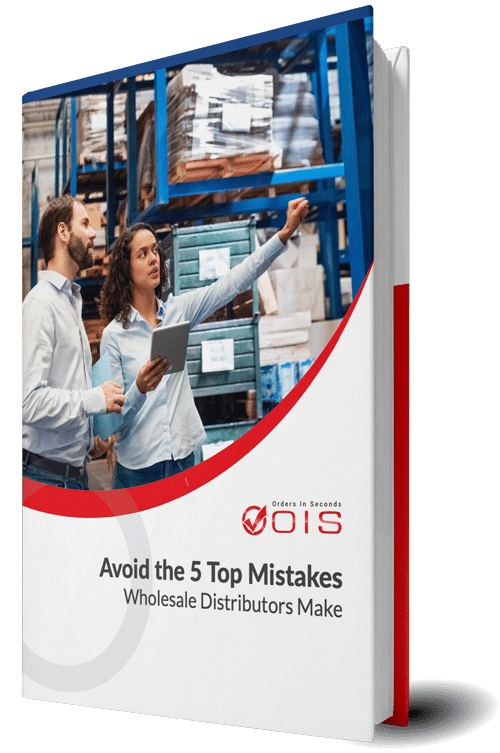
Avoid the Top 5 Mistakes Wholesale Distributors Make
Transportation and Logistics
Proximity to major transportation hubs such as airports and highways promotes efficient shipping and reduces logistics expenses. The choice of a warehouse location should take into account the availability of diverse transportation modes such as:
- rail
- intermodal
- marine
- truck
- pipeline
Tailor the transportation modes to the goods being handled.
A strategic location near various transportation methods can lead to increased shipping volumes and reduction in transportation costs.
Proximity to Customers and Suppliers
Locating a warehouse near your customer base and suppliers can provide several benefits, including:
- Decreased transportation costs
- Speeding up delivery times
- Enhancing market penetration
- Reducing the risk of supply chain hiccups
Furthermore, being close to transportation carrier services can optimize customer satisfaction by meeting high delivery expectations.
Exploring Different Types of Warehouses
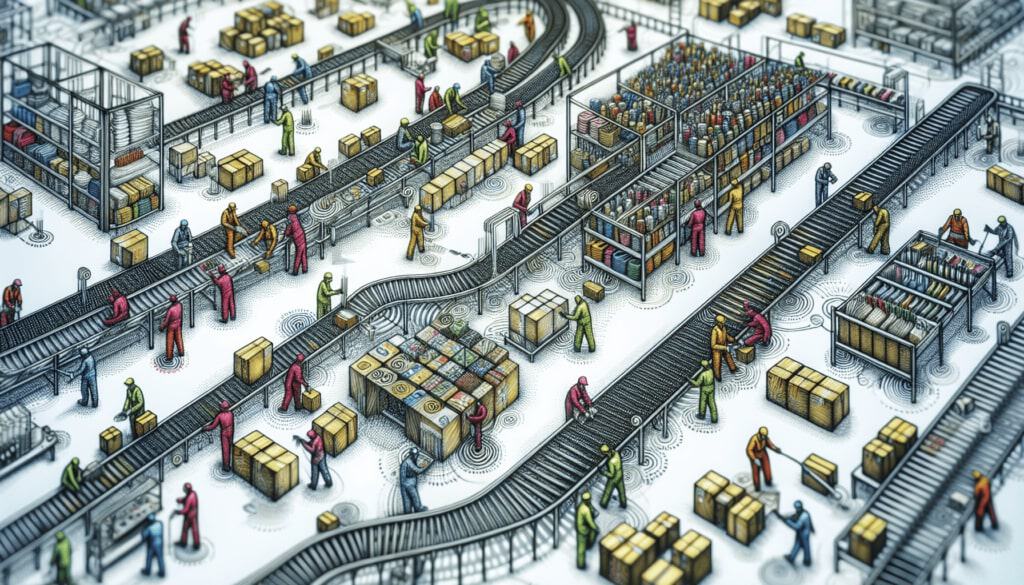
Having identified your warehouse needs and the factors for choosing an ideal location, it’s time to delve into the various types of warehouses.
There are numerous types of warehouses used in logistics and supply chain management, each designed to meet the specific needs of different business models. Among these, you will find traditional warehouses, flex spaces, and distribution centers, each with its unique characteristics and advantages.
Traditional Warehouses
Traditional warehouses offer the following advantages:
- Basic storage services
- More cost-effective, providing a clear understanding of financial commitments due to inclusive rental costs without hidden charges
- Adjustable lease terms that can be tailored to specific business needs, with options available for short-term leases as brief as 90 days.
A variety of unit sizes are offered in traditional warehouses, ranging from as small as 250 square feet to as large as 5,000 square feet.
Flex Spaces
Flex spaces are modern properties that offer a blend of industrial and office space, accommodating various business activities under one roof. These multi-purpose facilities seamlessly integrate warehousing with additional functionalities like dedicated office areas and showrooms, supporting diverse operational requirements.
The design of flex spaces can be tailored to meet specific business requirements, offering an adaptable solution for companies looking for a mix of uses from their warehouse rental.Distribution Centers
Distribution centers are specialized facilities designed for the efficient intake, sorting, and rapid redistribution of goods, playing a crucial role in the supply chains of retail businesses. Advanced distribution centers utilize smart warehouse technologies, including automation, robotics, and artificial intelligence, to reduce the need for human intervention and streamline logistics processes.
To ensure the efficiency and accuracy of operations, distribution centers conduct regular inventory inspections, utilizing technology like scanner systems to match deliveries with purchase orders and prevent inventory shrinkage.
Navigating Lease Agreements
After exploring the different types of warehouses, you should now focus on understanding the lease agreements. Warehouse lease agreements come in various forms such as modified gross leases, triple net leases, and full-service leases. It’s crucial to understand these different lease types, key terms, and conditions before entering into an agreement.
Types of Leases
In a triple net lease, tenants are responsible for covering operating expenses, which often results in lower rent compared to other leasing options. A modified gross lease, on the other hand, is a hybrid wherein tenants pay base rent plus a proportional share of some operating costs, while the landlord covers others. A full-service lease generally involves the landlord covering all property expenses, with the tenant only paying base rent, although tenants may share in operating costs above a set threshold through an expense stop.
Key Terms and Conditions
Rent and security deposit are key financial components of a warehouse lease that need to be clearly understood. The duration of the lease and termination conditions, such as penalties for early termination or subleasing options, should be reviewed to maintain flexibility.
Restrictions on property alterations and the terms governing leasehold improvements should be verified with the site owner to be compatible with necessary business operations, ensuring that a certain word in the agreement doesn’t hinder the process.
Searching for Available Warehouse Spaces
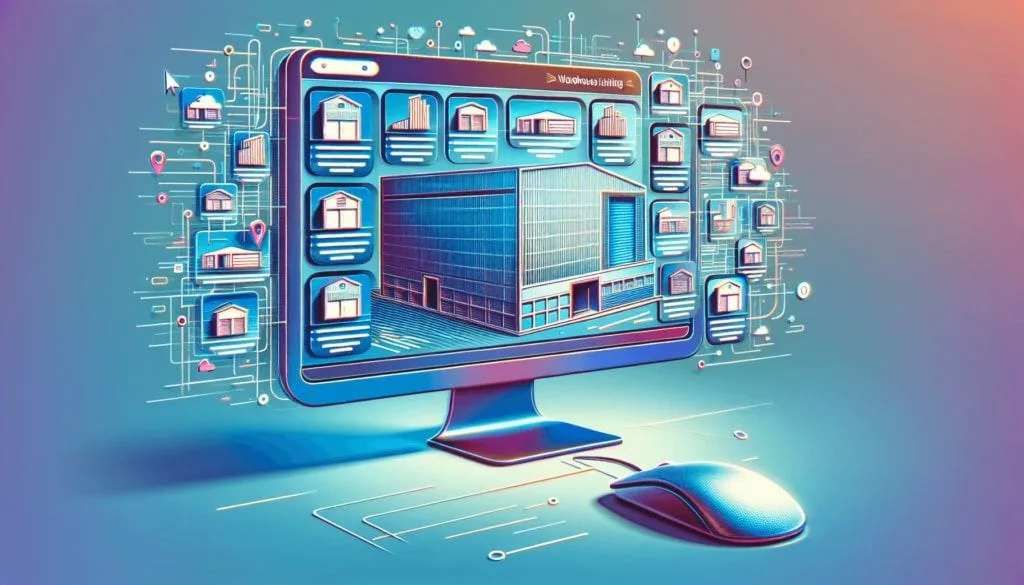
Armed with a clear understanding of your warehouse needs, the ideal location, the types of warehouses, and lease agreements, you should now commence your search for available warehouse spaces. Creating a searchable online presence for commercial spaces is essential as many potential tenants initiate their warehouse search via the internet.
Various platforms can be used to find small warehouse spaces, with options available through online listings on specialized real estate websites and by reaching out to commercial real estate firms.
Online Listings
Commercial real estate databases such as CoStar, LoopNet, and Commercial Exchange are frequently used by business owners to start their search for warehouse spaces. These platforms list commercial spaces, including small warehouses, for rent, offering:
- Fixed monthly rates
- 24/7 security
- On-site management
- Amenities
Networking and Referrals
While online listings are a great resource, don’t forget the power of networking and referrals. Engaging a commercial real estate broker with specialization in industrial properties and local insights is crucial for accessing a wider selection of warehouse rentals.
Forming connections within local business communities and commercial real estate networks often leads to valuable referrals for finding suitable warehouse spaces for small businesses.
Drive-By Searches
Last but not least, consider the good old-fashioned method of drive-by searches. Drive-by searches for small warehouse spaces in the SF area can uncover opportunities for businesses to grow by moving inventory out of homes and into dedicated storage areas.
In-person searches can reveal small warehouses that may offer additional amenities such as loading docks and organizational infrastructure aiding in efficient operation.
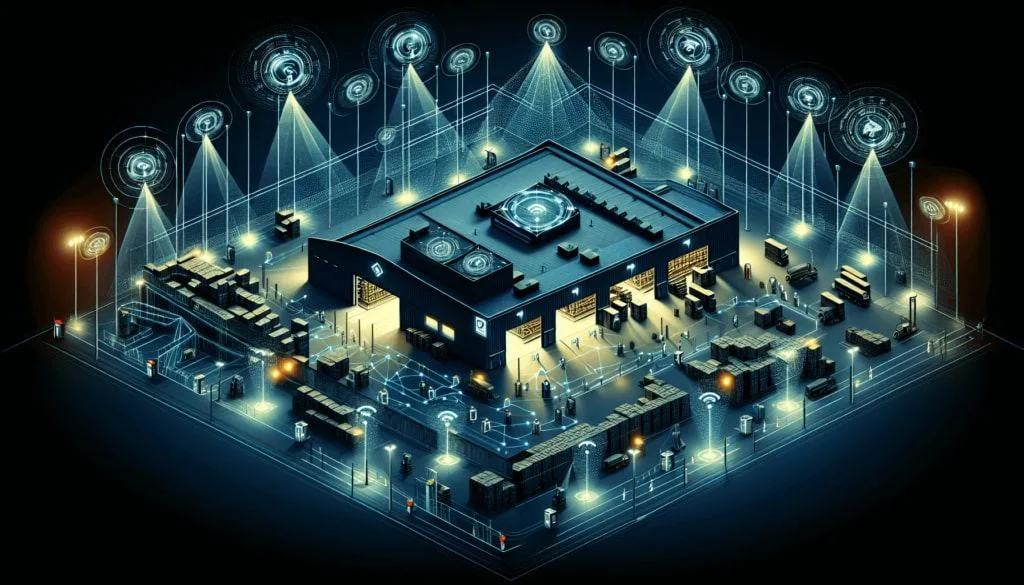
Upon identifying potential warehouse spaces, the next step is to assess them. This involves conducting physical inspections, assessing infrastructure and utilities, and reviewing security and safety features. Each of these aspects plays a crucial role in ensuring that the warehouse space meets your business needs and operational requirements.
Physical Inspections
The physical condition of a warehouse is an important aspect to consider. This involves inspecting the structural integrity, existing damage, and maintenance issues. It’s recommended to conduct an annual inspection, focusing on the condition of windows, floors, ceilings, and doors to prevent safety hazards.
Safety systems such as fire alarms, sprinkler systems, and fire extinguishers should also be inspected annually to guarantee a secure environment for warehouse inventory.
Infrastructure and Utilities
Infrastructure and utilities are another critical aspect of a warehouse. Adequate infrastructure such as electrical and plumbing systems is essential in a warehouse space. Utilities should be assessed for their capacity and reliability to ensure they meet the operational needs of the business.
Regular preventive maintenance for electrical systems should occur at least every three years or more frequently in harsh environments.
Security and Safety Features
Last but not least, security and safety features are a crucial part of a warehouse. Traditional warehouse properties are generally equipped with standard security features such as 24-hour CCTV monitoring and access control systems.
Implementing a robust warehouse security system can further safeguard valuable inventory through real-time surveillance, intrusion detection, and remote access management.
Regular security patrols and background checks on warehouse staff can also minimize internal theft risks by employing a reliable security service, which is an essential part of a comprehensive security solution.
Negotiating Lease Terms and Finalizing the Agreement
After evaluating potential warehouse spaces, you should proceed to negotiate the lease terms and finalize the agreement. Review the lease carefully upon approval, ensuring you understand all commitments.
Acquire liability and property insurance as required by the lease for renting traditional warehouses.
Negotiation Strategies
To strengthen negotiating power, business owners should conduct thorough market research to understand current warehouse rental rates. Inquiring about available inducements, such as free rent periods or financial aid for renovations, can provide additional negotiation power, especially in cases where the warehouse has been on the market for an extended period.
Considering the long-term implications of the lease, including costs and benefits, positions business owners to negotiate more favorable terms that align with their strategic goals.
Legal Review
Consulting a specialized commercial lawyer for lease agreement review is essential. This legal expertise helps in:
- Avoiding unforeseen expenses
- Providing a clear understanding of lease obligations
- Verifying that the lease adheres to local legal requirements
- Safeguarding the business from potential legal complications.
Preparing for Move-In
Before moving in, make sure to complete the following steps:
Secure all necessary permits that may be required for warehouse operation.
Acquire the proper insurance policies for the warehouse to cover potential risks involved in storage and operations within the premises.
Finalize any details with the landlord, ensuring all terms are met.
Confirm that the property is ready for occupation.
Arrange for utility services such as water, electricity, gas, and internet to be connected and fully functional for when the business operations commence.
Summary
In conclusion, finding the perfect warehouse space involves understanding your warehouse needs, choosing an ideal location, exploring different types of warehouses, navigating lease agreements, searching for available spaces, evaluating potential warehouses, negotiating lease terms, and preparing for move-in. Each step is crucial and requires careful consideration. By following this comprehensive guide, you’re well on your way to securing the perfect warehouse space that aligns with your business needs and operational requirements.
Frequently Asked Questions
To determine the size of the warehouse you need, calculate the square footage required for inventory storage, packing supplies, equipment, staff workspace, and loading areas, adjusting for utilization rate. Then, create a 2D visualization of the space to calculate the total storage area.
Different types of warehouses include traditional warehouses, flex spaces, and distribution centers, each tailored to meet specific business requirements.
How do I evaluate a potential warehouse space?
To evaluate a potential warehouse space, conduct physical inspections to assess its condition, structural integrity, and maintenance, while also reviewing its infrastructure, utilities, security measures, and safety systems. This will give you a comprehensive understanding of the property’s suitability for your needs.
Make sure to look for key terms such as rent, security deposit, lease duration, and maintenance responsibilities in the lease agreement. Understanding these terms and their implications is crucial for a successful lease agreement.
Before moving into a warehouse, ensure you have obtained all necessary permits, insurance, and finalized details with the landlord. Also, arrange for utility services to be connected and fully functional (date not necessary).
Optimize Your Wholesale Business Operations with Orders In Seconds
Finding the perfect warehouse space for rent is key for ensuring streamlined logistics and operational efficiency. However, success in the wholesale business relies on a combination of factors beyond just space, including efficient order processing.
Orders In Seconds (OIS) offers a solution to optimize order-taking processes with the OIS Pro App. With features like at hand inventory visibility, daily KPI report and a route manager reps can place orders stress-free. By integrating effective warehouse practices with tools like OIS, businesses can achieve comprehensive optimization across their entire operations. Book a free demo today to learn more about how OIS solutions can enhance your business efficiency!