Essential to warehouse efficiency and customer satisfaction, “what is order picking” is a question that can be answered as follows: order picking is the process of retrieving and preparing goods for shipment to fulfill specific customer orders. Its importance cannot be overstated, with a major portion of operational expenses devoted to this task. As we unpack what is order picking, you’ll learn not only its fundamental role but also get a glimpse into the strategies that power fast and accurate deliveries, setting the stage for the detailed exploration ahead.
Key Takeaways
- Order picking is a main expense in warehouse operations, heavily influencing customer satisfaction and corporate profitability, with various strategies like single order, batch, and zone picking being pivotal for efficiency and scalability.
- Advanced picking methods and combining strategies, such as wave picking and zone-batch-wave picking, add sophistication to warehouse processes, helping businesses handle modern logistics demands and improve workflow optimization.
- Automation and smart picking tools revolutionize the order picking process by boosting efficiency and accuracy, with automation including voice picking systems and mobile scanners, while adherence to best practices ensures streamlined operations for enhanced productivity.
Table of Contents
- Decoding Order Picking: The Backbone of Warehouse Operations
- Essential Techniques in Order Picking
- Advanced Picking Methods: Enhancing Efficiency and Accuracy
- Optimizing the Order Picking Process with Combined Strategies
- The Role of Automation in Order Picking
- Enhancing Your Warehouse's Racks with Smart Picking Tools
- Best Practices for Perfecting the Picking Procedure
- Maximizing Productivity Through Picking Preferences
- The Financial Implications of Picking Processes
- Summary
- Frequently Asked Questions
- OIS Inventory: Conquer Order Picking with Speed and Accuracy
Decoding Order Picking: The Backbone of Warehouse Operations
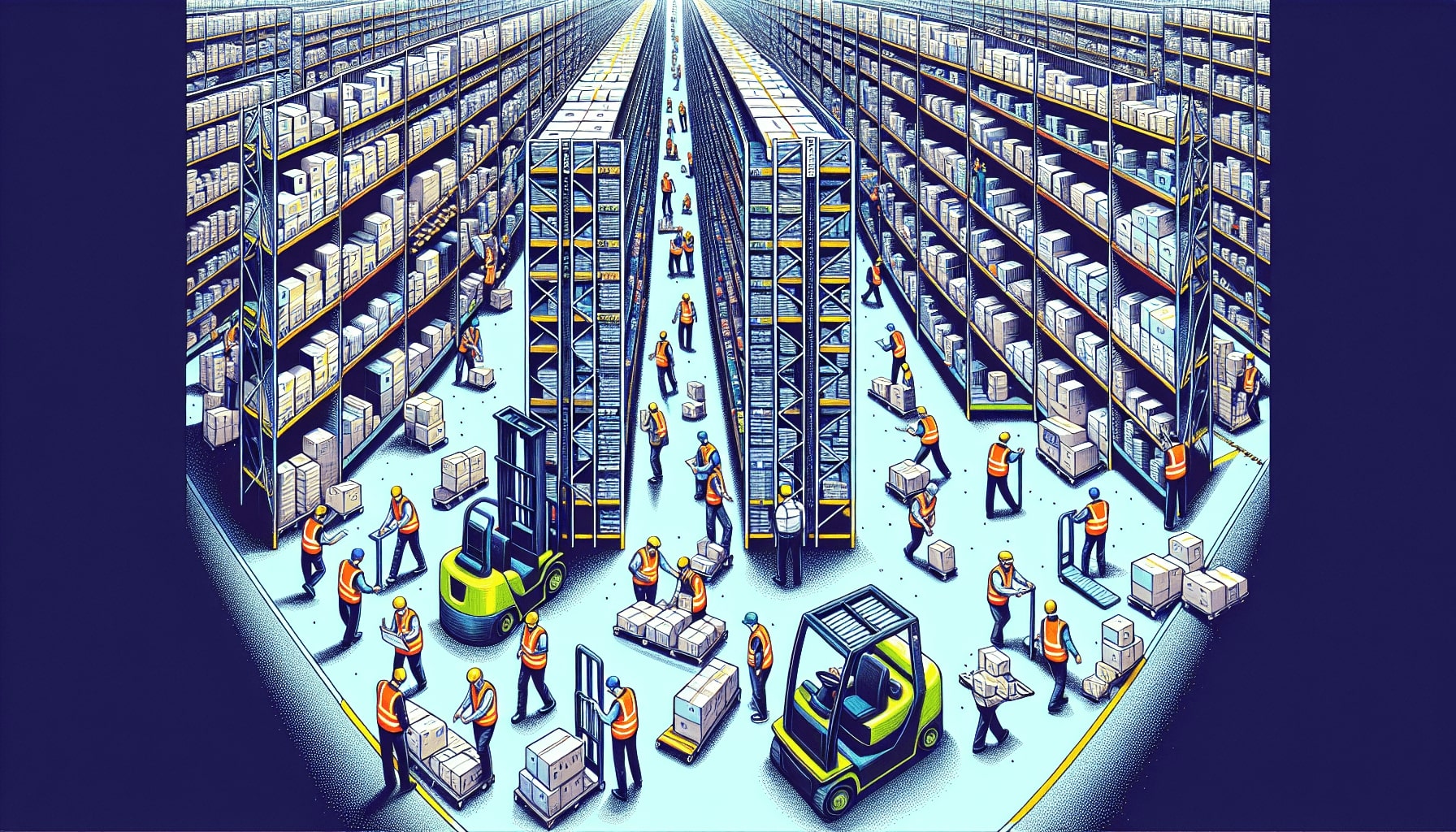
At the heart of any warehouse operation lies the intricate process known as order picking, or warehouse picking. It’s here that the rubber meets the road, where warehouse workers, or “pickers,” navigate through aisles to fetch the items that make up customer orders. This meticulous process isn’t just a matter of hauling products off shelves; it’s an art form that balances speed with accuracy, directly affecting a business’s bottom line and customer contentment.
Consider this: an estimate of 63% of a warehouse’s total operating expenses (Estimated by Georgia Tech. industry report) can be attributed to the act of order picking. Such a significant investment demands efficiency and flexibility, especially during those peak times when order volumes surge and the warehouse needs to scale up swiftly. An adept order picking system isn’t just about keeping costs down; it’s about ensuring that every package leaves the warehouse on time and complete, upholding a company’s reputation and driving profitability.
Essential Techniques in Order Picking
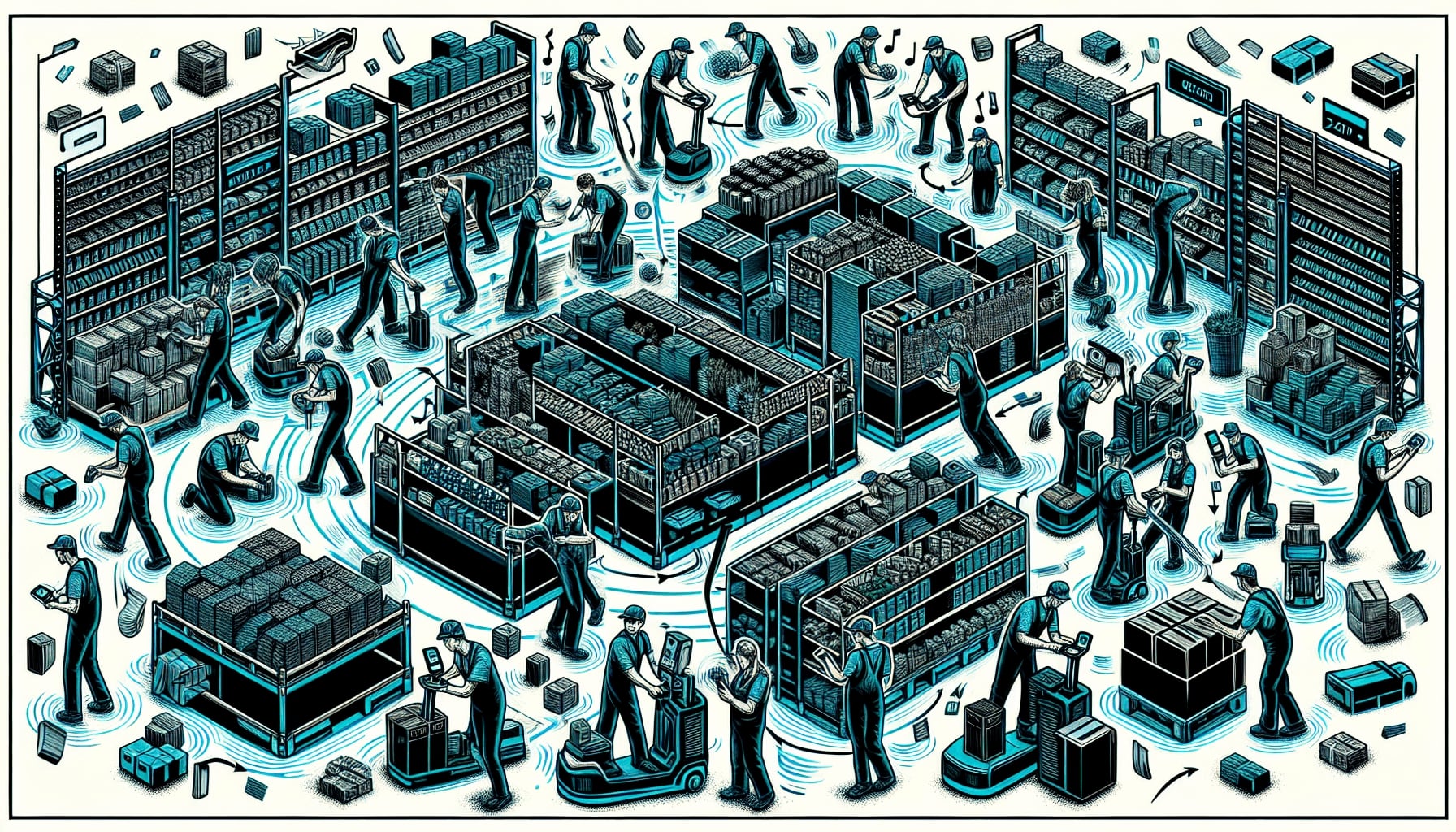
The warehouse is a chessboard, and order picking is the game where strategy reigns supreme. Mastering this game involves a variety of techniques, each with its own set of rules and benefits.
From the meticulous single order picking to the harmonious flow of batch and zone picking, these methods are the essential building blocks that keep the gears of warehouse operations turning.
The Single Order Strategy
When it comes to the single order picking strategy, envision a craftsman meticulously working on a unique piece, dedicating their full attention to a single masterpiece. In similar fashion, the single order picking method involves the careful selection of items for one order at a time, making it the go-to strategy for smaller warehouses that manage a more modest stream of orders. Often employed in business environments where the frequency of orders is lower, this technique stands out for its simplicity and its ability to keep operations streamlined.
However, single order picking isn’t just about simplicity; it’s about the personal touch. It’s ideal for those operations with a diverse range of SKUs in smaller quantities, where the focus on one order can ensure unparalleled accuracy and customer satisfaction. In that sense, it represents the form of order picking that closely mirrors the bespoke services of bygone eras, tailored to the needs of today’s smaller but no less important warehouse operations, taking into account each customer’s personal preference.
Mastering Batch Picking
Batch picking is akin to a conductor leading an orchestra: one movement directs multiple instruments, creating a symphony of efficiency. Here, pickers handle multiple orders at once, each order like a unique instrument in the overall performance. By focusing on one SKU at a time across various orders, batch picking simplifies the process and allows for a concerted effort that maximizes productivity, especially when dealing with high order volumes and frequent orders with common SKUs.
This method is a powerful force multiplier, allowing pickers to complete several orders concurrently, transforming what would be a series of solo performances into an ensemble that sings of speed and effectiveness. It’s particularly beneficial for warehouses bustling with activity, where common items are often sought after and the clock is always ticking. By mastering batch picking, companies can navigate the complexities of high-demand periods with grace and agility.
Zone Picking Dynamics
Zone picking turns a warehouse into a well-oiled machine, with each picker operating within their designated realm like a specialist in their field. By partitioning the warehouse into distinct zones and assigning pickers to these domains, zone picking sharpens both efficiency and accuracy in fulfilling orders. It’s a strategy that thrives on high-volume orders, where the choreography of pickers working in tandem across the warehouse floor results in a seamless flow of goods.
But the beauty of zone picking lies in its ability to adapt. With pick-and-pass processes, items can be passed from one zone to the next, allowing for a continuous and effective movement of goods through the warehouse. Pickers become deeply familiar with their zones, honing their skills and knowledge of the products they handle, which in turn minimizes errors and speeds up the order fulfillment process. It’s a dynamic environment where each player knows their part and performs it with precision, ensuring that the right item always reaches the right hands.
Advanced Picking Methods: Enhancing Efficiency and Accuracy
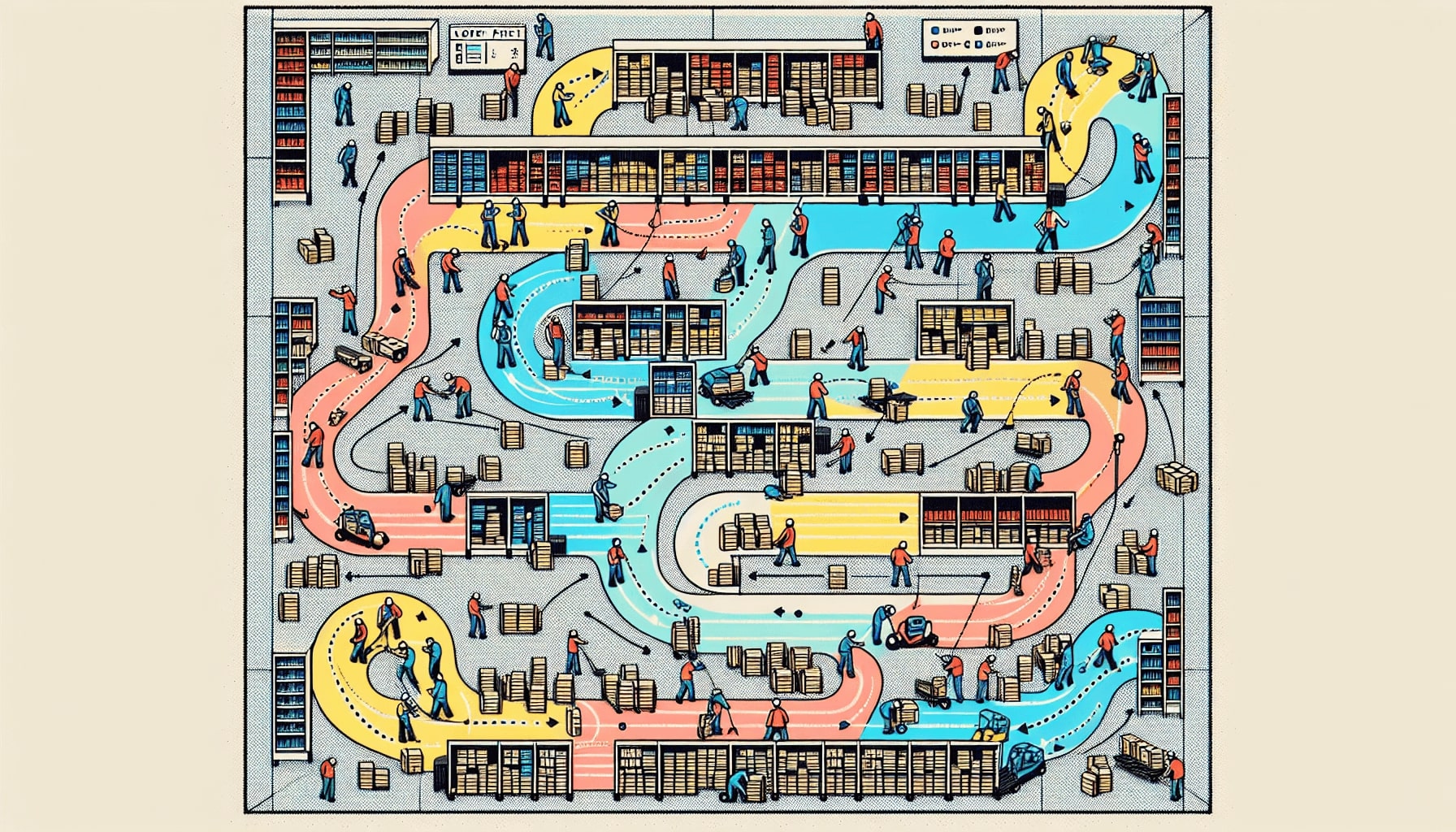
As warehouses evolve, so too do the methods employed to keep them running at peak performance. Advanced picking methods, such as wave, case, and pallet picking, represent the next step in the evolution of warehouse efficiency. They build upon the foundation laid by the essential techniques, adding layers of sophistication and precision that can handle the complexities of modern-day logistics.
These methods aren’t just incremental upgrades; they’re transformative approaches that reimagine the warehouse as a more agile, responsive entity. Some of these methods include:
- Static zone picking: capitalizes on the expertise of dedicated pickers for each zone, enhancing accuracy and reducing the learning curve for new employees.
- Dynamic zone picking: offers the flexibility to adjust in real-time to changing order profiles and demand, ensuring a balanced workload and minimizing bottlenecks.
- Rotational zone picking: merges the best of both worlds, allowing for picker specialization while maintaining adaptability to various inventory zones, thus ensuring that pickers are well-versed across the warehouse.
Wave Picking Explained
Wave picking is the maestro of the warehouse, organizing the picking schedule like a conductor times the orchestra, ensuring that each section plays its part at the right moment. By grouping orders into time windows, it enables the simultaneous collection of items for multiple orders in a single trip, optimizing resource use and boosting daily order fulfillment rates. In particular, for items that are difficult to access or require heavy lifting equipment, bulk wave picking can be a godsend, streamlining the process in ways that individual piece picking simply cannot match.
However, wave picking does come with its own set of challenges. It requires a coordinated effort from all warehouse zones and may necessitate additional resources during the sorting and consolidation phase. But for companies that deal with a higher number of picks per order, the structured approach of wave picking, which segments the work into manageable pieces and aligns with outbound carrier deadlines, can make all the difference in meeting the demands of a fast-paced market.
Case and Pallet Picking Demystified
When it comes to case and pallet picking, think of it as wholesale shopping for the warehouse — bulk is the name of the game. In pallet picking, entire pallets of goods are moved in one swoop directly to the packing area, embodying efficiency in its purest form. Case picking, on the other hand, involves selecting products in full case quantities, which are then typically placed onto pallets, carts, or conveyors for transportation. This method is particularly useful when dealing with a large number of SKUs that require smaller quantities per SKU, ensuring that large orders can be filled with rapid precision.
In the realm of case picking, the goal is to heighten pick density and minimize travel time, often achieved by picking to multiple pallets at once. By executing this strategy effectively, warehouses can streamline their operations and swiftly deal with bulk orders that represent a significant portion of their business. It’s a method that rarely gets it wrong, typically providing a reliable and efficient means to handle the heavy lifting of warehouse order fulfillment.
Optimizing the Order Picking Process with Combined Strategies
Much like a chef blending ingredients to create the perfect dish, combining picking strategies can concoct a recipe for success in the warehouse. By integrating techniques such as batch or zone picking, warehouses can achieve a synergy that leads to more simultaneous picks and a faster, more efficient order fulfillment process.
Take, for instance, the integration of batch and cluster order picking. This strategy streamlines the picking process by allowing workers to scan and process a group of cartons all at once, saving precious time and energy. Similarly, incorporating product kitting and assembly into the order picking strategy enables the concurrent sale and processing of kitted items alongside individual ones, elevating operational efficiency to new heights.
The Split Pick and Pack method is another example of strategic synergy, grouping products from multiple orders to be picked at the same time, with tasks divided either sequentially or among separate teams for picking and packing.
Synergy of Zone Batch Picking
Zone-batch picking is where the precision of zone picking meets the collective strength of batch picking. In this strategy, order pickers are designated to specific zones within the warehouse, where they then carry out batch picking within their assigned area. It’s akin to each picker being a chef in their own kitchen, whipping up multiple dishes at once, all while ensuring that each one is perfectly cooked.
By focusing their efforts within a specific zone, pickers can handle multiple orders simultaneously, ramping up the speed of order fulfillment and making the most of the warehouse’s spatial layout. Cluster picking, a part of this strategy, allows pickers to collect multiple items for different orders in one go, cutting down on the walking distance and amplifying productivity. It’s a compelling approach that takes the strengths of two effective strategies and merges them into one powerful, cohesive system.
The Fusion of Zone Wave Picking
Envision zone wave picking as a strategy that orchestrates the meticulous timing of wave picking with the specialized expertise of zone picking. Pickers are assigned to their zones and are responsible for collecting SKUs for all orders within that zone during predetermined time slots. This ensures that each picker can concentrate on their area of the warehouse, diving deep into their inventory knowledge and maximizing their efficiency.
The strength of zone wave picking lies in its adaptability. Warehouse zones are established based on a plethora of variables, including assortment attributes and operational insights, all of which can be enhanced by picking technologies. This strategy demonstrates flexibility by adapting to inventory changes and seasonal demands, sometimes using dynamic zoning and pop-up zones to meet the fluctuating needs of the warehouse.
Zone-batch-wave picking, in particular, combines several order picking methods, allowing pickers to handle multiple orders in their designated zone within a scheduling window, optimizing the overall workflow.
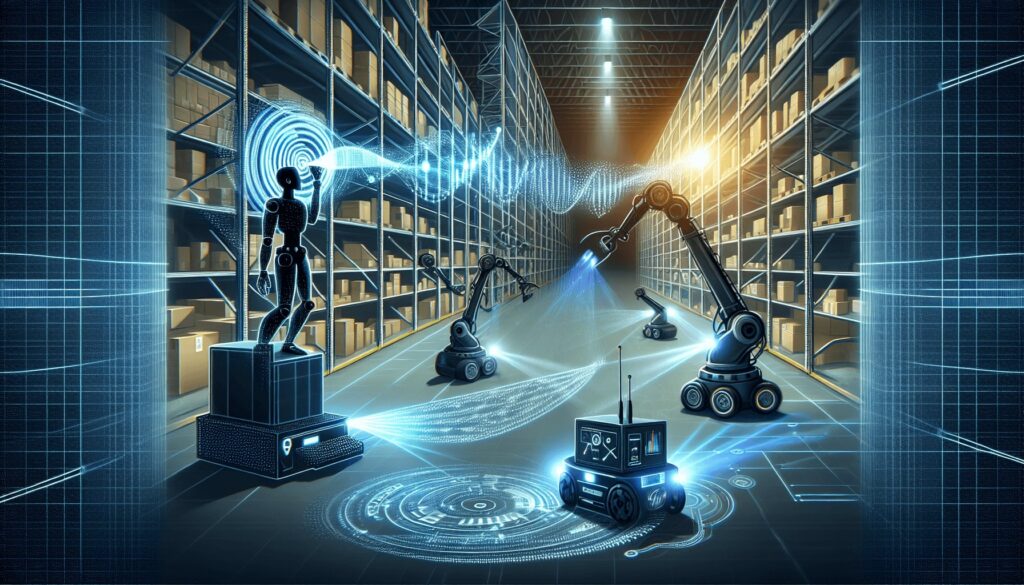
The advent of automation in order picking has been nothing short of revolutionary, propelling the process into a new era. Automated picking systems, seamlessly integrated with warehouse management software, not only provide real-time inventory visibility but also optimize picking routes, taking efficiency to unprecedented levels.
Automation extends its reach into every nook and cradle of the warehouse, from:
- Workflow automation software that systematizes processes
- Robotic picking systems that harness cutting-edge computer vision and gripping technologies for high-speed, precise tasks
- The AutoStore system, which bolsters zone picking with a fleet of robots that manage item retrieval, thus reducing physical strain and enhancing efficiency.
Collaborative robots, or cobots, work alongside human pickers, augmenting their abilities and providing a less labor-intensive operation that retains adaptability in different picking scenarios.
The Impact of Voice Picking Systems
Voice picking systems are like the personal assistants of the warehouse world, guiding workers with vocal cues that enhance both the mobility and safety of the picking process, especially when paired with warehouse security cameras etc. By employing speech recognition and synthesis, these systems allow workers to receive verbal instructions, freeing their hands and eyes to focus on the task at hand, which can significantly improve safety and efficiency.
The beauty of voice picking systems lies in their ability to streamline operations without the need for pickers to constantly refer to paper lists or handheld devices. This hands-free approach means pickers can concentrate better on accurately gathering items and navigating the warehouse’s racks, leading to fewer errors and a smoother picking process overall. It’s a testament to how voice technology can transform a traditional warehouse operation into a more agile and responsive business.
If mistakes are holding back your wholesale business, download our free eBook “Avoid the Top 5 Mistakes Wholesale Distributors Make” and discover key strategies to optimize your operations for success!
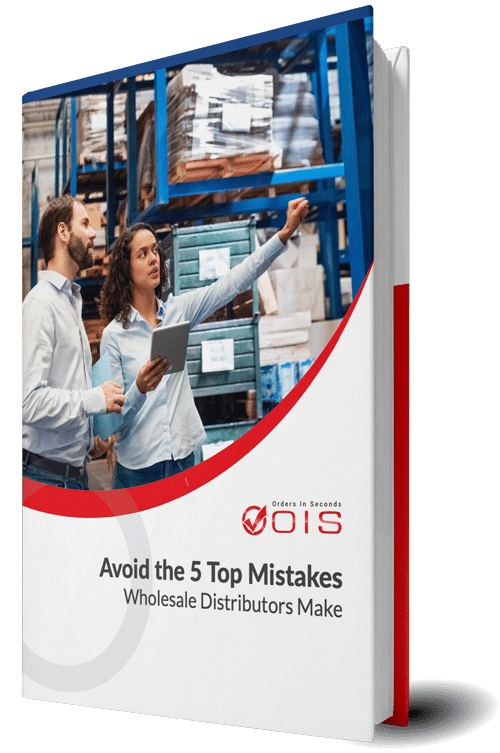
Avoid the Top 5 Mistakes Wholesale Distributors Make
Mobile Scanner Picking: A Game-Changer
Mobile scanner picking is revolutionizing the way pickers interact with orders, equipping staff with the technology to receive real-time data and make informed decisions on the fly. This method leverages scan verification technologies to significantly reduce errors, ensuring that the right products are selected for each order with pinpoint accuracy.
The implications of mobile scanner picking are vast:
- It streamlines the order fulfillment process by negating the need for later quality checks
- It minimizes the travel time required to locate items
- Scanners provide immediate access to picklists and item locations, allowing pickers to navigate the warehouse’s landscape with confidence
- This level of efficiency translates to saved time and money, making mobile scanner picking a smart investment for any warehouse looking to stay competitive in today’s market.
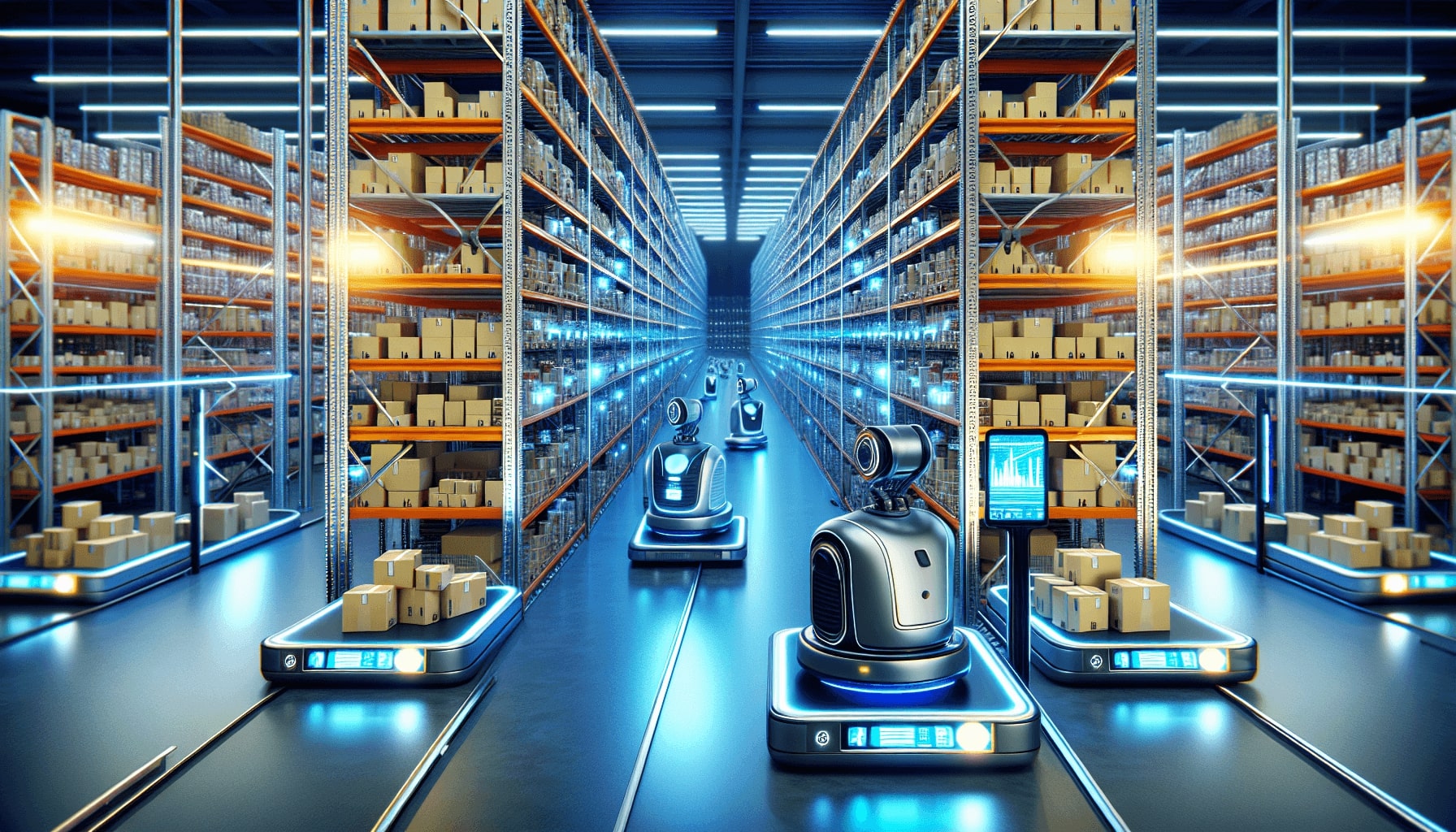
Smart picking tools are the secret weapons that can significantly up the ante in a warehouse’s order picking process. Imagine having smart weight scales that can instantly verify if an order’s weight matches the expected tally, thereby reducing errors and predicting shipping costs with greater precision. Such tools not only prevent issues with over- or under-packaging of orders but also streamline the entire shipping process.
Then there are collaborative mobile robots, or cobots, which are designed to work alongside human workers, guiding them through the picking process with unerring accuracy. These robotic assistants can lead to a less labor-intensive and more efficient picking operation, allowing human workers to focus on more complex tasks that require a personal touch.
By integrating advanced technologies like these into warehouse racks, businesses can significantly enhance the productivity and accuracy of their order picking process, paving the way for a smarter, more sophisticated warehouse environment.
Best Practices for Perfecting the Picking Procedure
To perfect the picking procedure, it’s critical to adhere to a set of best practices that optimize every aspect of the operation. This includes:
Designing the warehouse layout to mirror the natural inventory flow from receiving to shipment, avoiding unnecessary backtracking and improving overall efficiency.
Strategically placing frequently picked items for easy access.
Picking directly into shipping cartons to reduce travel time within the warehouse.
Scheduling replenishment of fast-moving items to ensure pickers always have stock at hand, eliminating delays and enhancing productivity.
By following these best practices, you can optimize your picking process and improve overall efficiency in your warehouse.
Inventory profiling based on item velocity allows for the products to be placed strategically, optimizing the efficiency of the picking process. Additionally, the use of bins, totes, and dividers can facilitate the quick location of items, especially smaller ones, and enhance space utilization. Adopting storage strategies like slotting can further refine warehouse operations by reducing accidents, congestion, and retrieval times. These best practices not only streamline operations but also contribute to cost-effective warehouse management.
Maximizing Productivity Through Picking Preferences
The human element plays a pivotal role in maximizing productivity within the order picking process. By integrating ergonomics, such as minimizing physical stress from heavy lifting and bending, warehouses can see a marked improvement in picker efficiency and productivity. Personalizing the work environment with ergonomic tools and accommodating picker preferences not only leads to improved job performance but also reduces the risk of injuries, ensuring a happier and more effective workforce.
To elevate productivity, establishing a method where order items are touched only once is essential. This prevents errors and negates the need for repacking or rechecking, which in turn enhances overall productivity in the picking process. Optimizing item location by utilizing the ‘golden picking zone’, an ergonomic area between the knees and shoulders, helps in reducing the time spent on each pick, allowing pickers to move faster and more comfortably through their tasks.
The Financial Implications of Picking Processes
The ripple effect of optimized order-picking systems on a company’s finances is profound. By reducing labor hours, minimizing operational errors, and improving inventory management, such systems can lead to significant cost reductions. Efficient warehouse order picking strategies include:
- Zone picking
- Discrete picking
- Batch picking
- Wave picking
These strategies streamline the process by decreasing travel time, reducing congestion, and enhancing the overall speed of operations.
Mobile scanner picking, in particular, enhances fulfillment accuracy by providing real-time picklist data and locations, which helps eliminate errors in the picking process. Additionally, measuring key performance indicators is essential for benchmarking and pinpointing areas that need improvement within the picking process, thereby achieving financial efficiency.
In essence, the warehouse picking process can be a major determinant of a warehouse’s profitability, and its optimization should be a top priority for businesses looking to improve their bottom line.
Summary
From the meticulous single order strategy to the symphony of batch picking, and from the advanced technologies of automation to the strategic incorporation of combined picking strategies, the art of order picking is a complex tapestry woven with precision, efficiency, and innovation. It is clear that order picking is not merely a step in the supply chain; it is the linchpin that holds the entire operation together, directly impacting customer satisfaction and financial success. As warehouses continue to embrace new technologies and methodologies, the future of order picking shines bright, promising ever-greater levels of sophistication and productivity.
Frequently Asked Questions
Order picking is crucial for efficient warehouse operations, customer satisfaction, and overall profitability as it involves retrieving items to fulfill customer orders, impacting operating costs significantly.
Single order picking involves selecting items for one order at a time, making it ideal for smaller warehouses with lower order volumes, while batch picking handles multiple orders concurrently, efficiently suited for high order volumes with common SKUs.
Can you explain zone picking and its benefits?
Zone picking is a warehouse strategy that assigns pickers to specific zones, improving efficiency and accuracy for high-volume orders by allowing pickers to specialize in their designated areas.
Automation plays a crucial role in order picking by optimizing picking routes, providing real-time inventory visibility, and reducing manual labor through technologies such as voice picking systems, mobile scanner picking, and robotic assistance. This leads to improved efficiency and accuracy in the order picking process.
Optimizing the order picking process can lead to cost reductions, minimize errors, and improve inventory management, ultimately positively impacting a company’s bottom line.
OIS Inventory: Conquer Order Picking with Speed and Accuracy
Order picking can make or break your warehouse’s efficiency. As you’ve seen, even small improvements in picking strategies can lead to significant cost reductions and happier customers.
Stop wasting time and money on manual picking errors! Get to know OIS Inventory, a cloud-based app specifically designed for wholesalers and distributors.
It automates order picking with barcode scanning, ensuring accuracy and eliminating wasted time from picking mistakes. This user-friendly app integrates seamlessly with QuickBooks, streamlining your picking workflows and boosting overall warehouse efficiency.
Schedule a free demo today to see how OIS Inventory can help you conquer order picking and achieve significant cost savings!